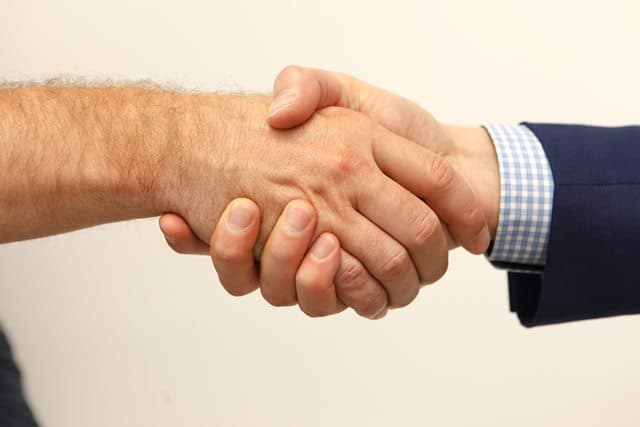
Quality Agreements with Third Party Manufacturer
- Kazi
- Last modified: April 2, 2024
All products that are produced at a Third Party Manufacturer (TPM) must be in compliance with Quality Policies & Standards, cGMPs, and all other applicable regulatory requirements. It is also required that there be as part of all new and renegotiated contractual business agreements with TPMs, a specific section of the business contract that clearly defines the quality related requirements, and roles and responsibilities of the parties entering the contract.
This section of the contract will be clearly labeled as the Quality Agreement. This Quality Agreement must be developed and finalized at the time of the signing of the TPM Business Agreement. Quality Assurance is responsible for ensuring that a Quality Agreement is in place for each TPM Business Agreement.
Standard Requirements Establishing Quality Agreement
TPM Selection and Approval
QA or their designee, will participate in the selection process for all proposed TPM’s.
QA or their designee will perform an initial evaluation audit of potential new TPMs based on Quality Policies & Standards, cGMPs and all applicable regulatory requirements and issue an audit report. This audit report will document all observations, potential issues and pertinent information for any TPM under consideration.
Based on the audit report, QA or their designee will recommend either approval or rejection of the proposed TPM. In some cases, conditional approval may be recommended subject to completion of agreed upon corrective actions.
TPM Business Agreement
QA or their designee will review and approve all TPM Business Agreements to assure that all the quality aspects of the agreement are properly included and addressed. A Quality Agreement must be included as part of all TPM Business Agreements. A generalized Quality Agreement template is included at the back of this article. This template is designed for use as a basis for developing the final Quality Agreement and all aspects of the template may not apply to each Business Agreement.
210 SOPs, 197 GMP Manuals, 64 Templates, 30 Training modules, 167 Forms. Additional documents included each month. All written and updated by GMP experts. Checkout sample previews. Access to exclusive content for an affordable fee.
Ongoing QA Responsibilities & Support
All TPMs will be subject to periodic quality audits by QA or their designee. The results of all quality audits will be documented and communicated to the appropriate parties.
All products manufactured at TPMs will be tested, evaluated and released by the appropriate QA/QC group. QA may delegate these functions and services to the TPM and/or other designee. Delegation of any QA/QC assigned functions or services, must be documented and approved by the head of quality.
The appropriate QA/QC group must routinely evaluate all functions and services delegated to the TPM and/or other designee. Programs will be developed and implemented by the appropriate QA/QC group to qualify the TPM and/or designee to perform the above mentioned QA/QC functions and services.
Change Control
All proposed changes to the Quality Agreement must be reviewed and approved by QA Management or their designee prior to implementation.
QA or their designee will evaluate all significant changes in personnel, facilities, and/or degree of compliance at the TPM. Based on this evaluation, QA or their designee will recommend continuance and/or cancellation of the contract.
Any proposed changes in the processing or testing of products at the TPM must be reviewed and approved by QA Management or their designee prior to implementation.
Other areas of review:
Responsibility for Stability
Responsibility for Recalls
Responsibility for FDA or other governmental notifications
Responsibility for annual updates
Responsibility for filing updates (beyond annual)
Standard Quality Agreement Template
This Quality Agreement is a required and integral part of the Business Contract between the Contract Giver (Your company name) and the Contract Taker (Third Party Manufacturer).
Purpose of the Quality Agreement
This agreement outlines the responsibilities of the Contract Giver (CG) and Contract Taker (CT) with respect to the Quality Assurance of the product(s) referenced in the Business Contractual agreement. The CT agrees not to subcontract any of the manufacturing, packaging, labeling, testing, release and/or handling of the CG product(s) unless prior written authorization is obtained from the CG. The CG has the right and option to suspend and/or cancel the contract if the CT does not comply with any of the requirements of the Quality Agreement.
A matrix of responsibilities included at the end of this document delineates the primary responsible party for the various aspects of this Quality Agreement. (For each section of the agreement add detailed information and attachments as required).
Quality Agreement Specific Information (Information to be included here may be redundant with that in the Business Contract as this is intended to be a stand alone dynamic document)
This Contract is:
Valid from: (This date should be identical to the date on the Business Contract for given products)
Valid to: (This date should be identical to the date on the Business Contract for given products)
Between:
The Contract Giver (CG) or Licensee: (List Company Name, Location, Phone and Fax numbers)
The Contractor Taker (CT) or Licenser: (List Company Name, Location, Phone and Fax numbers)
This Quality Agreement was:
Prepared By:
(Appropriate Person or Persons Name, QA/QC Organization, Title, Company, Location, Phone and Fax Numbers, Signature and Date)
Approved By:
CG Representative(s): (Appropriate Person or Persons Name, Title, QA/QC Organization, Company, Location, Phone and Fax Numbers, Signature and Date)
CT Representative(s): (Appropriate QA/QC Person or Persons Name, Title, Company, Location, Phone and Fax Numbers, Signature and Date)
Note: there must be at least one representative approval from both the CG and the CT in this section.
The Primary Contact People are: (Appropriate QA/QC Person or Persons Name, Title, Company, Location, Phone and Fax Numbers at both the CG and CT sites must be listed here. It is the responsibility of the CG and CT to keep this contact list up to date.)
Abbreviations and Definitions of Terms
Abbreviations
Certificate of Analysis: COA
Contract Giver: CG
Contract Taker: CT
Detailed Material List: DML
European Union: EU
Current Good Manufacturing Practices: cGMPs
Not More Than: NMT
Product Quality Reviews: PQR
Qualified Person: QP
Third Party Manufacturer: TPM
Validation and/or Qualification: VQ
(Note: If other abbreviations are used in the Quality Agreement, they should be added to this section.)
Definitions of Terms
All general terms used in the Quality Agreement are defined in the cGMPs.
(Note: Where appropriate, more specific terms and the definitions used in the Quality Agreement should be added to this section.)
Change Control
All changes in this Quality Agreement and/or any quality related attachments, must be documented as an Addendum to the original Quality Agreement and reviewed and approved by representatives of Quality Assurance from the CG and CT.
The CT will utilize a documented system of procedures for the control of changes to packaging materials, raw materials, suppliers, equipment, manufacturing methods, product and material specifications and requirements, sampling, test methods, and release requirements. Any significant changes whether planned or unplanned shall be reviewed and approved by the CG prior to implementation.
All updates to regulatory applications related to the CG product(s) are the responsibility of the official holder of these applications, be it the CG or the CT. The official holder of the applications should be documented in this Quality Agreement. The CG or CT will provide all necessary information that it may possess, pertinent to the CG product(s), to the CT or CG to keep the regulatory file current and up-to-date.
Materials
Procurement and Delivery of Materials
The use and procurement of all the materials must be made by the CT as described in the DML provided by the CG. If a specific supplier of any material is indicated in the DML, the CT must always obtain the material from stated supplier. If a stated supplier is unable to supply material of sufficient quality or quantity, the CT must contact the CG for directions on how to proceed. Only after prior authorization has been obtained in writing from the CG, can the CT utilize an alternate supplier. In some cases, an alternate supplier of materials may need to be qualified via an audit, testing of sufficient batches of material, etc. prior to its use. This qualification could be conducted by either the CG or the CT as specified by the CG or as mutually agreed upon.
If the CT is responsible for determining a suitable source of a material and procuring it from this source, which is only allowed if specified in the DML, the source of this material must be communicated to the CG and documented by the CT.
Inspection and Testing of Materials
The material inspection plans and testing procedures provided by the CG or as mutually agreed upon between the CG and CT must be utilized by the CT. The results of this inspection and testing must be in accordance with specifications provide by the CG or as mutually agreed upon between the CG and CT.
Upon receipt, all containers of materials will be inspected by the CT for external condition, intact & authentic seals and compliance of the type and number of containers/labeling with the delivery documents. Materials must be inspected and/or tested on a batch-by-batch basis unless otherwise specified by the CG. If specified in the DML, some starting materials may be accepted and released by the CT utilizing the COA with abbreviated or no additional testing.
Retention, Storage and Handling of Materials
The CT agrees to sample and retain sufficient amounts of all materials except water, compressed gasses and any highly volatile compounds. The amount of retained samples is specified in the DML.
The CT agrees to store and handle the materials and retained samples under appropriate conditions that will assure they will comply with all the quality specifications provided by the CG. If special storage conditions are necessary for any materials, they will be noted by the CG on the DML. The CT agrees to comply with all special storage conditions. In the case of product labeling materials, the CT agrees to store them under appropriate controlled and secured conditions as stated by the CG or as mutually agreed.
Under no circumstances should any other materials which may present a potential hazard to the raw materials utilized in the CG products, such as beta-lactam and cephalosporin antibiotics, certain potent hormones, cytotoxic compounds, highly potent drugs, biological preparations or non-pharmaceutical chemicals, be stored in the same facility in proximity to the area utilized for the CG materials. If such materials are stored in the same facility the CG and CT must agree to their separation and segregation.
Specification(s) of the Product(s)
The referenced product(s) must be manufactured, packaged, labeled and handled according to the written specification(s) and procedures provided by the CG or as mutually agreed upon between the CG and CT.
Manufacturing and Packaging of the Products
The manufacturing and packaging of the product(s) will be done according to the specific procedures and instructions provided by the CG or as mutually agreed upon between the CG and CT.
All specific requirements for manufacturing equipment, manufacturing environment, equipment cleaning and storage, line clearance, certification of the manufacturing area, certification & training of the manufacturing personnel, laboratory equipment, laboratory environment and certification & training of the testing laboratory personnel will be supplied by the CG or as mutually agreed upon. The CT agrees to meet and comply will all of these requirements.
Under no circumstances should any other products which may present a potential hazard to the CG products, such as beta-lactam and cephalosporin antibiotics, certain potent hormones, cytotoxic compounds, highly potent drugs, biological preparations or non-pharmaceutical chemicals, be manufactured, processed, packaged or stored in the same facilities used for the CG product(s). Storage of products containing any potentially hazardous component shall be sufficiently isolated and segregated from the product(s) manufactured for the CG. The CT shall make the CG aware of the presence of any potentially hazardous products and mutual agreement is required between the two parties as to adequate storage. Any regulatory restrictions on storage of different types of products shall be adhered to.
The manufacturing and packaging of the CG product(s) by the CT must be in adherence to the specifications supplied by the CT or as mutually agreed upon and in compliance with all SOPs, GMP’s and any other applicable regulatory requirements. The CT will prepare, for each batch of product manufactured for the CG, the complete manufacturing and packaging batch documentation as agreed upon between the CG and CT. This complete documentation must be retained by the CT in accordance with appropriate document retention schedules as provided by the CG. This documentation must be readily accessible for review and inspection by the CG and/or regulatory authorities if requested.
Any waste product or labeling materials should be destroyed in a secure and legal manner, preventing unauthorized use and/or environmental problems.
Inspection and Testing of the Product(s)
The inspection and testing of the product(s) is carried out by either the CT or the CG (or both) as agreed upon and documented.
If the CT performs some or all of the inspection and testing, the CT will provide to the CG a COA and any other associated inspection and testing documentation for each batch of product manufactured. The CG reserves the right to inspect and/or test all batches of the subject product(s) produced by the CT prior to release and distribution.
Notification and Approval of Deviations
The CT must notify the CG within 2 working days from time of discovery whenever there is a significant deviation from stated procedures or stated specifications. A significant deviation is defined as any Out-Of-Specification result and/or any manufacturing, packaging, labeling or testing deviation that may effect the quality, safety or efficacy of the product(s). Reprocessing would always be considered a significant deviation. All deviations will be investigated and fully documented by the CT. This documentation will be retained as part of the batch documentation for the batch affected. When deemed necessary, the CG reserves the right to request additional or more in-depth investigation of the deviation by the CT. In all cases when a significant deviation occurs on a batch, the CG will have the final review and decision making responsibility as to the impact of the deviation(s) on the product(s) which will include the disposition of the affected lots.
Release and Shipment of the Product(s)
The Final Release of the product(s), which is defined as the release to the marketplace, is the responsibility of the CG. The CT has the responsibility to Release the product(s) to the CG. The CT will not ship any of the CG product(s) to any destination until they are Final Released by the CG unless prior approval has been received from the CG to perform such shipments. In EU countries, the Final release has to be performed by a QP as defined by the CG. The Final Release Authority may be delegated from the CG to the CT on a product by product basis. This delegated Final Release Authority must be appropriately documented and approved by the CG. The CG reserves the right to withdraw the delegated Final Release Authority from the CT at any time.
Retained Samples of the Product(s)
The CT agrees to store Retained samples for all product(s) unless otherwise agreed upon between the CG and CT. These retained samples will include both the Internal Reference samples and Regulatory Reference samples. The amount of Retained samples will be specified by the CG and provided to the CT. The CT agrees to store the retained samples under appropriate product label storage conditions and in a secure area for a period of time as defined by the CG.
Storage of Product(s)
The CT agrees to store the CG product(s) under appropriate product label storage conditions and in a secure area to insure that they comply with all the quality specifications and attributes. If special storage conditions are necessary for any CG product(s), they will be noted and supplied by the CG to the CT. The CT agrees to comply with any special storage conditions.
Stability Activities
The responsibility for stability testing, data interpretation, reporting, and updating stability information to regulatory documents for the subject product(s) will be proposed by the CG and agreed upon by the CG and CT. This agreement will be documented. All of the stability-related activities that the CT is responsible for, will be completed in a timely manner.
Process Validation and Qualification of the Product(s)
The process, manufacturing and control procedures (including cleaning procedures where applicable) need to be validated and qualified by the CT in the facility the CT intends to utilize to manufacture the CG product(s), using the equipment the CT intends to utilize and with the personnel the CT intends to employ to make the CG product(s).
Typically, a VQ Protocol document is created with input from both the CT and the CG. This VQ Protocol contains all the required activities and the acceptance criteria and is documented. This VQ Protocol is executed on at least the first three batches of product(s) produced by the CT for the CG unless otherwise agreed upon between the CG and CT. If there are any problems during the execution of the VQ Protocol, they must be immediately communicated to the CG. If the problems cannot be resolved, the VQ Protocol must be repeated on additional batches until at least three consecutive batches of CG product(s) meet all the specifications. Any problems encountered during the execution of the VQ Protocol must be documented by the CT.
All of the related validation/qualification documents will be assembled in a Validation Summary Report and provided to the CG for review and approval. The CG will determine and document (in this section) whether the VQ Protocol primary data and documentation will be maintained by the CT or CG.
Annual Product Quality Review(s)
Responsibilities for annual PQR shall be agreed upon between the CG and the CT and documented (in this section). All PQR activities, which are the responsibility of the CT, will be completed and documented in a timely manner. The PQR documentation completed by the CT, will be provided to and/or available for the CG to review.
The CG and CT will meet periodically to review quality issues related to the obligations and responsibilities as described in this Quality Agreement. During this periodic review, quality issues related to the past production by the CT of the CG product(s) will be reviewed. The information presented and discussed during this review meeting will be documented by the CT and approved by the CG.
Complaints on the Product(s)
The CG will typically receive, communicate with the customer(s) and close all complaints related to the referenced product(s). The CT will provide any complaint information received (from customers in the marketplace and/or regulatory authorities) to the CG in NMT 7 days unless a more urgent need is recognized such as in the case of a potential tampering or adverse medical event. Upon the request by the CG, the CT will investigate the complaints as required and provide a written report on the results of the investigation to the CG in NMT 30 working days or sooner if required by the CG. The CG will communicate with the customers and/or the regulatory authorities the results of the complaint investigation if necessary. The CG reserves the right to delegate any or all the part(s) of the complaint handling process the CG normally handles (i.e., receipt, communication with the customer and closure of complaints) to the CT on a product by product basis.
Returned Goods
The specific handling of Returned Goods will be specified and documented by the CG if required.
Recall of the Marketed Product(s)
In the event that recall, withdrawal, or field correction, of the subject product(s) is required because the product violates applicable laws, regulations, agreed upon specifications, or is deemed unacceptable for some other reason, whether or not such action is requested by any governmental agency, the initiating party shall notify the head of Quality Assurance of the other party. In the conduct of the recall, withdrawal, or field correction, the parties shall fully cooperate in notifying customers and conducting the necessary activities. If the recall is initiated due to a defect in the subject CG product(s) arising from a failure attributable to negligence or oversight by the CT, then the CG will be completely reimbursed by the CT for the manufacturing expenses of all the CG product(s) affected as well as all recall and associated expenses.
Audits and Inspections of Facilities and Product(s)
The CT will notify the CG of any inspections or actions by regulatory agencies or other enforcement bodies which could potentially impact the CG product(s). The CT will provide the CG with the results of all such regulatory audits in NMT 7 days.
The CG reserves the right to audit the CT’s facilities and systems as they relate to the manufacture and control of the CG products(s). These audits may be performed on a periodic basis at times mutually agreed upon by the CG and CT. The right to audit will also cover any subcontractors (e.g. a contract laboratory) if utilized by the CT. The CG also reserves the right to be present at the CT during the manufacture of the CG product(s) and/or during the inspection of the CG product(s) by any regulatory agencies.
The auditing of the suppliers of all materials utilized in the manufacture and packaging of the CG product(s) will be the responsibility of the party, CG or CT, that provides said items for the final CG product(s). The results from audits of material suppliers conducted by the CT, covering materials to be used on the CG product(s), will be provided to the CG for review if requested.
Quality Agreement Distribution of Responsibility Matrix
Section No. | Section Name | Responsible Party | |
CG | CT | ||
1. | Purpose of the Quality Agreement | ||
2. | Quality Agreement Specific Information | ||
3. | Abbreviations and Definitions of Terms | ||
3.1 | Abbreviations | ||
3.2 | Definitions of Terms | ||
4. | Change Control | ||
5. | Materials | ||
5.1 | Procurement and Delivery of Materials | ||
5.2 | Inspection of Testing of Materials | ||
5.3 | Retention, Storage and Handling of Materials | ||
6. | Specifications of Product(s) | ||
7. | Manufacturing and Packaging of the Product(s) | ||
8. | Inspection and Testing of the Product(s) | ||
9. | Notification and Approval of Deviations | ||
10. | Release and Shipment of the Product(s) | ||
11. | Retained Samples of the Product(s) | ||
12. | Storage of Products(s) | ||
13. | Stability Activities | ||
14. | Process Validation and Qualification of the Product(s) | ||
15. | Annual Product(s) Quality Review | ||
16. | Complaints on the Product(s) | ||
17. | Returned Goods | ||
18. | Recall of the Marketed Product(s) | ||
19. | Audits and Inspections of Facilities and Product(s) |
Copies of specific documents referenced in each section should be attached.
Author: Kazi Hasan
Kazi is a seasoned pharmaceutical industry professional with over 20 years of experience specializing in production operations, quality management, and process validation.
Kazi has worked with several global pharmaceutical companies to streamline production processes, ensure product quality, and validate operations complying with international regulatory standards and best practices.
Kazi holds several pharmaceutical industry certifications including post-graduate degrees in Engineering Management and Business Administration.
Documents requirement